Keselamatan Makmal: Penilaian dan Kawalan Risiko Penggunaan Mesin Gerudi Konvensional di Makmal Pengajaran dan Pembelajaran
Secara umumnya, bengkel atau biasa juga diistilahkan sebagai makmal pemesinan yang terdapat di institusi pengajian tinggi sering menjadi tumpuan para pelajar bagi menjalankan latihan amali dan menyelesaikan sesuatu projek atau tugasan yang melibatkan kerja-kerja pembangunan produk. Aktiviti pengajaran dan pembelajaran (PdP) yang berlangsung di makmal pemesinan ini tidak hanya bagi sesuatu kursus tertentu sahaja tetapi meliputi pelbagai kursus daripada pelbagai program. Ini mewujudkan suasana persekitaran kerja yang sentiasa dipenuhi oleh bilangan pelajar yang ramai pada satu-satu masa merangkumi aktiviti PdP yang berjadual dan juga yang tidak berjadual seperti projek tahun akhir, projek capstone serta projek-projek kursus yang melangkaui waktu kelas formal.
Cabaran utama yang timbul akibat keadaan ini adalah dalam memastikan aspek pemantauan yang berkesan ketika pelajar menjalankan sesuatu aktiviti di bengkel. Bilangan staf yang terhad ditambah tanggungjawab staf yang perlu melaksanakan pelbagai tugasan berbeza dalam satu-satu masa menjadi kekangan utama dalam hal ini. Lebih menyulitkan kerana rata-rata pelajar adalah pengguna baharu bagi sesuatu mesin yang mana memerlukan lebih tunjuk ajar dan pemantauan ketika melakukan kerja. Ditambah pula sering terdapat segelintir pelajar yang mengabaikan atau mengambil mudah berkenaan pematuhan kepada peraturan-peraturan dan kaedah kerja selamat yang ditetapkan.
Mesin Konvensional
Di kebanyakan bengkel pengajaran institusi pengajian tinggi atau institusi pendidikan dalam negara ini, mesin konvensional masih digunakan secara meluas dalam aktiviti PdP. Mesin konvensional biasanya dirujuk kepada mesin yang bersifat manual, tidak dikawal oleh komputer dan hanya dilengkapi komponen asas seperti motor, gear, tali sawat, mata alat dan sebagainya. Penggunaannya mudah namun kekurangan utama adalah ciri-ciri keselamatan pada mesin tersebut. Beberapa contoh mesin konvensional yang sering digunakan ialah seperti mesin larik, mesin kisar, mesin gerudi, dan mesin pemotong.
Dalam artikel ini, konteks perbincangan menjurus kepada penggunaan mesin gerudi konvensional. Mesin ini adalah antara mesin yang digunakan secara meluas di bengkel-bengkel PdP untuk kerja-kerja membuat lubang pada pelbagai bahan kerja seperti logam, plastik dan kayu. Komponen yang terdapat pada mesin gerudi secara asasnya ialah pembekal kuasa, motor, kepala pemutar (spindle head), chuck, mata gerudi, tapak dan pengendali (handle). Kaedah mengoperasi mesin gerudi ini ialah pembekal kuasa akan menggerakkan motor yang disambungkan kepada kepala pemutar. Mata gerudi yang dipasangkan kepada kepala pemutar akan berpusing mengikut kelajuan motor sama ada tetap atau boleh ubah bergantung kepada tetapan mesin. Pengendali digunakan untuk menggerakkan mata gerudi secara turun-naik menyentuh permukaan bahan kerja yang hendak ditebuk. Selalunya bahan kerja diikat pada alat pengapit supaya tidak bergerak ketika digerudi.
Bahaya Mesin Gerudi Konvensional
Bahaya merujuk kepada keadaan tidak selamat yang terdedah kepada seseorang. Dalam penggunaan mesin gerudi konvensional, potensi wujudnya keadaan bahaya ini lebih tinggi kerana ciri-ciri keselamatan mesin yang sangat minimum selain faktor daripada diri pengguna itu sendiri. Dalam satu kejadian kemalangan yang pernah direkodkan di sebuah bengkel pemesinan di UMPSA, seorang pelajar telah mengalami luka yang agak dalam pada jari dan menerima beberapa jahitan akibat terkena kepingan besi tajam yang terpusing ketika melakukan kerja menggerudi lubang pada kepingan besi tersebut. Punca langsung kemalangan tersebut adalah kerana pelajar terbabit tidak mengikat (clamp) kepingan besi menggunakan pengapit dan hanya memegang menggunakan tangan ketika menggerudi. Daya kilas yang tinggi di saat mata gerudi menyentuh permukaan kepingan besi tersebut menyebabkan ia berputar lalu mencederakan jari pelajar terbabit. Siasatan lanjut mendapati pengabaian prosedur berlaku kerana pelajar tersebut dalam keadaan tergesa-gesa untuk menyelesaikan kerja disebabkan kerja tersebut dilakukan setelah waktu operasi makmal berakhir. Manakala staf yang bertugas juga tidak dimaklumkan sebelum kerja hendak dilakukan. Ini adalah sebahagian contoh kemalangan yang telah berlaku akibat daripada pelanggaran prosedur oleh pelajar sendiri.
PENILAIAN RISIKO
Secara umumnya, penilaian risiko adalah proses penting dalam memastikan keselamatan di tempat kerja. Proses ini melibatkan pengenalpastian bahaya, menilai tahap risiko yang mungkin berlaku daripada segi keterukan dan kebarangkalian ia berlaku, seterusnya mengambil langkah untuk mengurangkan atau menghapuskan risiko tersebut.
Pengenalpastian Bahaya
Dalam konteks mesin gerudi konvensional, elemen bahaya dilihat dan dikenal pasti daripada tujuh kategori iaitu mekanikal, fizikal, ergonomik, elektrik, bahan kimia, kebakaran dan psikososial. Huraian terperinci bagi setiap kategori bahaya dinyatakan seperti berikut:
Bahaya Mekanikal
i. Kecederaan akibat sentuhan dengan mata gerudi: Bahaya utama adalah apabila tangan atau bahagian badan pengguna bersentuhan dengan mata gerudi yang sedang berputar. Ini boleh menyebabkan kecederaan serius seperti luka dalam atau kehilangan jari.
ii. Kepingan kerja terpusing atau tercabut: Jika kepingan kerja tidak diikat dengan betul menggunakan pengapit, ia boleh terpusing atau tercabut semasa proses penggerudian yang berpotensi menyebabkan kecederaan pada pengguna atau individu berhampiran. Ini sebagaimana contoh kejadian kemalangan yang dikongsi sebelum ini.
iii. Tersangkut pakaian atau rambut: Pakaian yang longgar atau rambut yang tidak diikat dengan kemas boleh tersangkut pada bahagian yang berputar, menarik pengguna ke arah mesin dan menyebabkan kecederaan serius. Oleh itu, pemakaian sarung tangan tidak digalakkan semasa mengendalikan mesin gerudi kerana sarung tangan juga berpotensi tersangkut pada bahagian berputar seterusnya menjadi punca kemalangan.
iv. Percikan serpihan logam: Proses penggerudian boleh menghasilkan serpihan logam kecil yang boleh terpercik ke arah pengguna, berisiko mencederakan mata atau kulit jika tidak dilindungi dengan peralatan perlindungan diri yang sesuai.
Bahaya Fizikal
i. Bunyi bising: Mesin gerudi konvensional menghasilkan bunyi bising yang boleh menjejaskan pendengaran jika terdedah dalam jangka masa yang panjang tanpa perlindungan telinga yang betul.
ii. Getaran: Pengendalian mesin gerudi yang lama boleh menyebabkan keletihan pada tangan dan lengan akibat getaran yang berterusan, berpotensi menyebabkan masalah kesihatan seperti gangguan saraf.
Bahaya Ergonomik
i. Posisi kerja yang tidak ergonomik: Postur atau kedudukan badan yang tidak sesuai ketika mengendalikan mesin gerudi boleh mengakibatkan ketegangan otot, sakit belakang, atau masalah postur.
ii. Pengendalian beban yang tidak sesuai: Mengangkat dan mengapit kepingan kerja yang berat atau besar tanpa alat bantu boleh menyebabkan kecederaan pada bahagian belakang dan sendi.
Bahaya Elektrik
i. Pendawaian yang rosak: Pendawaian atau soket yang rosak boleh menyebabkan kejutan elektrik kepada pengguna. Ini boleh mendatangkan kemalangan yang serius terutamanya dalam persekitaran yang basah atau lembap.
ii. Penggunaan peralatan elektrik yang tidak sesuai: Penggunaan wayar penyambung dan pembahagian kuasa yang tidak sesuai boleh menyebabkan lebihan beban (overloading) dan risiko kebakaran.
Bahaya Bahan Kimia
i. Pendedahan kepada pelincir atau minyak pemotong: Penggunaan pelincir atau minyak pemotong semasa penggerudian boleh menyebabkan kulit atau pernafasan terdedah kepada bahan kimia yang merbahaya. Ini boleh menyebabkan tindak balas seperti alahan, kegatalan kulit, atau masalah pernafasan.
ii. Kesan gas atau asap beracun: Dalam sesetengah keadaan, haba yang terhasil daripada proses penggerudian boleh menyebabkan bahan kimia atau pelincir mengeluarkan asap atau gas yang beracun.
Bahaya Kebakaran
i. Percikan api: Dalam keadaan penggerudian dilakukan pada bahan logam tertentu, percikan api mungkin terjadi. Ini boleh menyebabkan kebakaran terutamanya jika terdapat bahan mudah terbakar di sekeliling kawasan kerja.
ii. Mesin terlalu panas (overheat): Penggunaan mesin secara berterusan tanpa rehat terutama pada komponen motor dan mata gerudi boleh menyebabkan overheating, yang meningkatkan risiko kebakaran.
Bahaya Psikososial
i. Tekanan dan keletihan: Penggunaan mesin dalam tempoh yang panjang tanpa rehat boleh menyebabkan keletihan fizikal dan mental, meningkatkan risiko kesilapan yang boleh membawa kepada kemalangan terutamanya dalam situasi iaitu kerja-kerja dilakukan di saat akhir dan menghampiri akhir tempoh masa diberikan.
ii. Kurangnya fokus: Gangguan seperti bunyi bising atau keadaan persekitaran yang tidak selesa boleh mengurangkan fokus pengguna, meningkatkan kemungkinan berlakunya kemalangan.
Penilaian Tahap Risiko
Setelah bahaya dikenal pasti, langkah seterusnya ialah menilai tahap risiko terhadap setiap bahaya tersebut berdasarkan dua komponen utama; Kemungkinan berlakunya bahaya (likelihood) dan kesan atau impak (severity). Di UMPSA, panduan yang digunakan dalam menentukan kebarangkalian berlakunya risiko berdasarkan kadar kekerapan pendedahan seseorang terhadap bahaya tersebut. Secara ringkas ditunjukkan dalam Jadual 1, aras kebarangkalian diberikan markah bermula 5- sangat tinggi, 4-tinggi, 3- sederhana, 2- rendah dan 1- tidak mungkin.
Berpandukan kaedah penilaian tahap risiko yang diterangkan, beberapa contoh penilaian yang dibuat terhadap bahaya dalam penggunaan mesin gerudi konvensional boleh dihuraikan seperti berikut:
i. Bahaya Mekanikal- Kecederaan Akibat Sentuhan dengan Mata Gerudi
• Kebarangkalian: Tinggi (Skor: 5). Sentuhan dengan mata gerudi berputar boleh berlaku jika pengguna tidak mematuhi prosedur keselamatan atau tidak menggunakan alat pelindung diri dengan betul.
• Impak: Kritikal (Skor: 3). Kecederaan boleh termasuk luka dalam atau sehingga kehilangan jari dan sekiranya berlaku memerlukan rawatan perubatan dengan segera.
• Tahap Risiko: Tinggi (Skor 15)
ii. Bahaya Mekanikal- Kepingan Kerja Terpusing atau Tercabut:
• Kebarangkalian: Tinggi (Skor: 4). Berlaku jika kepingan kerja tidak diapit dengan betul terutama bagi pengguna yang tidak berpengalaman atau sengaja mengabaikan prosedur kerja yang betul.
• Impak: Sangat Kritikal (Skor: 4). Kecederaan serius boleh berlaku jika kepingan kerja terlepas dan terkena pengguna atau orang lain.
• Tahap Risiko: Tinggi (Skor:16).
iii. Bahaya Mekanikal- Tersangkut Pakaian atau Rambut:
• Kebarangkalian: Sederhana (Skor: 3). Risiko ini lebih tinggi jika pengguna memakai pakaian yang longgar atau rambut yang tidak diikat.
• Impak: Sangat Kritikal (Skor 4). Kecederaan boleh menjadi serius jika pengguna ditarik ke dalam mesin.
• Tahap Risiko: Sederhana (Skor: 12).
iv. Bahaya Mekanikal- Percikan Serpihan Logam:
• Kebarangkalian: Sederhana (Skor: 3). Serpihan logam kecil sering terhasil daripada proses penggerudian.
• Impak: Kritikal (Skor: 3). Kecederaan biasanya terhad kepada mata atau kulit jika tidak memakai alat pelindung diri.
• Tahap Risiko: Sederhana (Skor: 9).
KAWALAN RISIKO
Keputusan penilaian tahap risiko yang dibuat membawa kepada langkah seterusnya iaitu menentukan tahap tindakan berdasarkan tahap risiko yang dinilai. Pendekatan yang diguna pakai di UMPSA adalah berdasarkan Jadual 4, tempoh masa serta keperluan yang berbeza ditetapkan untuk langkah kawalan diambil berdasarkan tahap risiko. Contohnya bagi tahap risiko TINGGI, tindakan segera perlu diambil paling lama dalam tempoh tiga bulan bagi mengurang atau menghapuskan risiko tersebut.
Secara umumnya bagi tindakan pengawalan risiko, kaedah kawalan adalah berdasarkan hierarki kawalan yang mengaturkan langkah-langkah pencegahan secara berturutan bermula daripada yang paling berkesan hingga kepada yang paling kurang berkesan. Dalam hierarki kawalan risiko langkah tertinggi ialah penghapusan iaitu langkah untuk menghapuskan bahaya sepenuhnya daripada persekitaran kerja, seperti menggantikan proses atau melantik pihak ketiga untuk mengendalikan kerja tersebut. Jika penghapusan tidak dapat dilaksanakan, baharulah langkah pada peringkat kedua iaitu penggantian dipertimbangkan, iaitu bahaya yang dikenal pasti digantikan dengan alternatif yang kurang berbahaya, contohnya menggunakan peralatan yang lebih moden dengan ciri keselamatan yang lebih baik. Dalam sesetengah keadaan, langkah pengasingan boleh dilakukan iaitu melibatkan pemisahan fizikal bahaya daripada pengguna seperti menempatkan mesin berbahaya di bilik khas yang hanya boleh diakses oleh orang yang berkelayakan atau memasang pengadang untuk memisahkan bahaya daripada pengguna.
Sekiranya ketiga-tiga langkah ini tidak praktikal, kaedah kawalan kejuruteraan digunakan untuk mengubah persekitaran kerja atau mesin bagi mengurangkan risiko, seperti memasang pelindung atau pengadang pada mesin untuk mencegah sentuhan langsung dengan komponen bergerak. Selain itu kawalan pentadbiran turut boleh dilaksanakan yang melibatkan perubahan kepada cara kerja dan proses seperti memperkenalkan prosedur operasi standard (SOP), memberikan latihan keselamatan, dan menekankan amalan kerja yang selamat. Akhir sekali, pada peringkat terendah penggunaan peralatan perlindungan diri (PPD) adalah langkah terakhir dalam hierarki ini iaitu pekerja dilengkapi dengan peralatan seperti sarung tangan, cermin mata keselamatan, dan pelindung telinga untuk melindungi diri mereka daripada bahaya yang tidak dapat dihapuskan atau dikurangkan melalui langkah-langkah sebelumnya
Kawalan semasa
Berdasarkan pemerhatian di lapangan, bagi kerja yang melibatkan penggunaan mesin gerudi ini, kawalan risiko secara penghapusan, penggantian atau pengasingan agak kurang praktikal untuk dilaksanakan kerana proses kerja ini adalah sebahagian daripada keperluan pengajaran iaitu pelajar perlu belajar secara praktikal kaedah pengoperasian mesin tersebut. Manakala untuk menggantikan kepada mesin yang lebih selamat memerlukan bajet yang besar yang sukar untuk diperoleh.
Justeru langkah kawalan yang boleh dilaksanakan ialah secara kawalan kejuruteraan, kawalan pentadbiran dan penggunaan PPD. Bagi mesin gerudi konvensional, langkah kawalan kejuruteraan adalah pada tahap paling minima kerana mesin cuma dilengkapi dengan suis kecemasan, pengadang manual dan pengapit manual yang boleh diabaikan secara mudah. Oleh sebab itu, kebanyakan langkah kawalan semasa sering tertumpu kepada kawalan pentadbiran dan penggunaan PPD.
Di makmal dan bengkel kebanyakan institusi pendidikan misalnya, setiap mesin selalunya akan ditampal dengan dokumen SOP sebagai panduan kepada pelajar dalam menggunakan mesin dengan kaedah yang betul dan selamat. Sebelum itu kebiasaannya semua pelajar akan mengikuti taklimat keselamatan bengkel daripada staf bertugas dan akan diterangkan serta dilatih kaedah mengoperasi sesuatu alat atau mesin tertentu berpandukan SOP kerja yang ditetapkan.
Selain itu penggunaan papan tanda amaran dan papan tanda keselamatan juga merupakan salah satu langkah kawalan pentadbiran yang kerap diamalkan. Antara kaedah menarik yang digunakan di salah sebuah bengkel pemesinan di UMPSA ialah kaedah Single Point Lesson (SPL). SPL ialah kaedah latihan dan komunikasi yang digunakan secara meluas dalam industri untuk meningkatkan kesedaran keselamatan dan memperbaiki prosedur kerja terutamanya di tempat yang pernah berlaku kemalangan. SPL merupakan pendekatan pendidikan yang ringkas, fokus dan mudah difahami bertujuan untuk memberikan maklumat atau arahan mengenai satu topik khusus, biasanya berkaitan dengan keselamatan atau prosedur kerja.
PENAMBAHBAIKAN BERTERUSAN
Daripada pemerhatian terhadap kawalan semasa yang telah dilaksanakan, elemen yang perlu dan penting untuk ditambah baik adalah dari aspek kawalan kejuruteraan. Berbanding kawalan pentadbiran dan PPD, kawalan kejuruteraan adalah lebih berkesan terutama dalam situasi makmal PdP yang melibatkan pelajar yang ramai, tahap pemantauan yang rendah serta risiko kecuaian atau ketidakpatuhan terhadap prosedur yang tinggi.
Dalam konteks mesin gerudi konvensional misalnya, penggantian pengadang mesin manual dengan pengadang automatik yang dilengkapi pemasangan sensor keselamatan yang lebih canggih dapat meningkatkan keberkesanan kawalan risiko. Teknologi terkini membolehkan pengawasan automatik terhadap operasi mesin, iaitu sensor boleh mengesan sebarang pergerakan tidak normal atau akses yang tidak dibenarkan, lalu menghentikan operasi secara automatik.
Selain itu, dengan perkembangan teknologi terkini seperti Internet of Things (IoT) dan kecerdasan buatan (AI), penambahbaikan berterusan juga boleh melibatkan pengintegrasian teknologi maklumat dalam sistem keselamatan makmal. Sebagai contoh, pemasangan sistem pengawasan video dan penyimpanan data berkenaan operasi mesin membolehkan analisis data untuk mengenal pasti trend atau tingkah laku yang berisiko. Maklumat ini boleh digunakan untuk membuat keputusan yang lebih baik mengenai keperluan penambahbaikan kawalan kejuruteraan atau perubahan kepada prosedur keselamatan. Dalam jangka masa panjang, pendekatan proaktif ini bukan sahaja mampu mengurangkan risiko kemalangan tetapi juga memupuk budaya keselamatan dalam kalangan pelajar dan seterusnya membentuk amalan kerja yang selamat apabila mereka melangkah ke alam pekerjaan.
KESIMPULAN
Akhirnya, melalui perbincangan yang cuba dibawa, penulis mengharapkan pembaca terutamanya warga pendidik dan akademik yang terlibat dalam bidang pengajaran TVET menyedari cabaran yang dihadapi dalam memastikan aspek keselamatan di makmal dan bengkel PdP serta kepentingan melakukan penilaian dan mengambil langkah kawalan risiko yang berkesan. Penekanan juga cuba diberikan terhadap penambahbaikan aspek kawalan kejuruteraan iaitu kepakaran yang dimiliki oleh warga akademik dan penyelidik dalam bidang teknologi dapat diaplikasikan untuk menambah baik ciri-ciri keselamatan mesin-mesin konvensional seterusnya memberi manfaat dalam meningkatkan kualiti pengurusan keselamatan di makmal-makmal institusi pendidikan dan pengajian tinggi di dalam negara ini khususnya.
SEKALUNG BUDI
Artikel ini sebahagian daripada hasil penerbitan di bawah projek penyelidikan yang dibiayai oleh Geran Pembangunan Produk UMPSA (PDU213216). Penghargaan kepada semua pihak yang terlibat iaitu unit teknikal di Fakulti Teknologi Kejuruteraan Pembuatan dan Mekatronik (FTKPM) UMPSA, pihak pengurusan Unit Pengurusan Keselamatan dan Kesihatan Pekerjaan (OSHMO) UMPSA dan semua ahli kumpulan penyelidik.
RUJUKAN
1. Department of Occupational Safety and Health. (2022). Akta Keselamatan dan Kesihatan Pekerjaan (Pindaan) 2022 (Akta A1648). https://www.dosh.gov.my/index.php/ms/perundangan/akta
2. Department of Occupational Safety and Health. (2008). Garis Panduan bagi Pengenalpastian Hazard, Penaksiran Risiko dan Kawalan Risiko (HIRARC). https://www.dosh.gov.my/index.php/ms/perundangan/garispanduan/hirarc-1/
3. Unit Pengurusan Keselamatan & Kesihatan Pekerjaan (OSHMO).(2023). Slaid kursus Taklimat Pengisian HIRAO bertarikh 7 Ogos 2023.
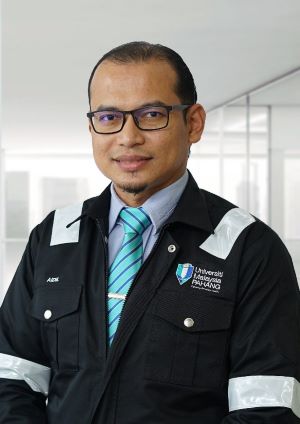
Penulis adalah Pegawai Latihan Vokasional Kanan dan Ketua Kluster Akademik, Pusat TVET Termaju, Universiti Malaysia Pahang Al-Sultan Abdullah (UMPSA). Beliau Berpengalaman hampir 15 tahun dalam pengurusan keselamatan makmal di Fakulti Teknologi Kejuruteraan Pembuatan dan Mekatronik (FTKPM), UMPSA.
E-mel: shafiza@umpsa.edu.my
- 1156 views